Stationary and rotating parts
While standard electric motors have a stationary housing and a rotating shaft, the opposite is true for drum motors. The shaft is stationary, it is fixed in a frame, flanged or otherwise mounted. The rotating part is the drum, which encloses the motor and gearbox. As a result, not only a relatively small shaft, but a large portion of the surface area is available for power transmission. The drum itself is a type of tube that can be very easily cut and fabricated to the size needed. Since the exterior rotates, the electrical supply must also be via one of the fixed shafts.
Internal structure of a drum motor
The internal structure of a drum motor is relatively simple. The motor is usually a three-phase, or more rarely a direct current, motor connected to the fixed shaft. As in any electric motor, a copper wire is wound into coils. When current flows through the winding, a magnetic field is generated, and this is converted into rotary motion. The motor is located inside the drum on the same side as the electrical supply. It turns a second shaft, which is located exclusively inside the drum motor and is oriented towards the center of the drum.
As it is common with electric motors, this rotary motion has a higher speed and lower torque than it is generally required for applications. Therefore, the motor is followed by a gearbox, the first gear of which is pressed directly onto the motor shaft mentioned earlier. The other gears of the gearbox are suspended inside the drum in such a way that they mesh, but do not touch the drum and remain unaffected by its rotation. The stages of the gearbox can be spur gears, or planetary gears. Oil filling inside the drum provides lubrication of the gears, in addition it dissipates the waste heat from the electric motor. Due to the encapsulated design, self-cooling by air flow is not possible as with a standard IEC motor. The lost heat is dissipated by the conveyor belt. The last gear wheel of the gearbox transmits the torque to a gear rim, which is attached to the inside of the drum. The rotation of this sprocket thus also causes the drum to rotate. This in turn drives the conveyor belt.
External characteristics of the drum
When selecting a drum motor, the speed at which a driven conveyor belt is to move in order to achieve the desired conveying performance is usually determined in advance. The belt speed is determined by three factors: By the speed of rotation of the motor, the transmission ratio of the gearbox and the diameter of the drum. With each revolution, the belt should always advance by exactly the circumference of the drum, so the belt speed accelerates as the diameter of the drum increases. Thus, the speed is not given in revolutions per minute, as is usual with other motors, but in meters per second. In case of a specific request, MOLL-MOTOR’s sales engineers will help with the conversion between these two values.
The conveyor belt can only move at the desired speed if it does not slip on the drum. Depending on the application, transfer can be satisfactorily achieved by the metal surface of the drum alone, or the surface can be provided with a coating of rubber or plastic. This coating can also have different profiles, in addition to smooth coating, there is also grooved to stabilize tracking, or diamond-shaped to increase friction. However, the friction between the drum and the conveyor belt should not be maximized, but should be precisely matched to the application to avoid unnecessary wear.
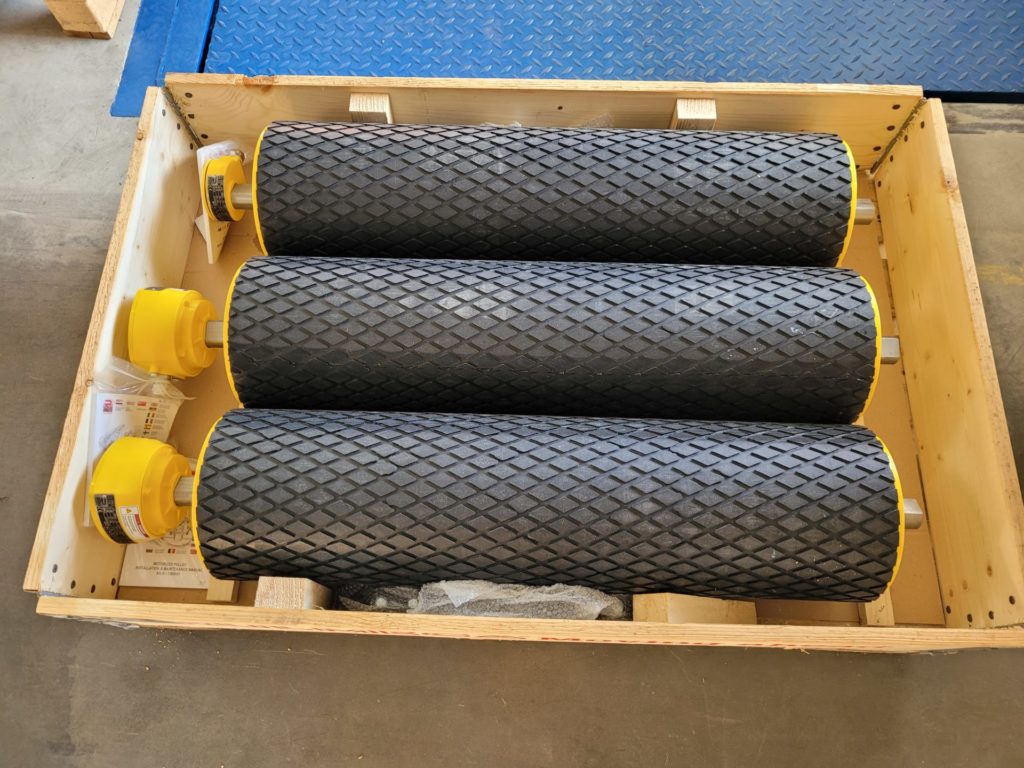
Main application Belt conveyors
Belt conveyors are often used in mining to convey various materials, such as coal, ore or overburden. These often have to be conveyed horizontally over long distances. The belt runs over both drum motors (drive rollers) and idlers, which do not contain a motor. The distance between the idlers must be chosen so that the belt does not sag or swing. The drum motors, in turn, are placed so that they provide uniform power transmission to the belt. A possible ratio of drive rollers to idlers is 1:10, in which case one drive roller would be used after every ten idlers. These rollers drive the belt and thus transport the material to its destination.
Drum motors are also used in many other industries, such as sunshade systems, cleaning brushes, in the packaging industry, in manufacturing for unwinding steel sheet rolls, and in the food industry. Drum motors are therefore popularly used to convey or process food products because they can be very well maintained. They are resistant to water jets and with the stainless steel surface they withstand aggressive disinfectants. Food grade lubricant fillings are used in the food industry. This prevents contamination of the food product in the event of a leak. These properties make them particularly hygienic. For example, drum motors are often used to transport fruit or vegetables on sorting belts, and they are also used to transport confectionery and baked goods to the next processing step.
Drum motors are thus an inconspicuous, yet relatively widespread niche product in our industry. Our first choice for drum motors is the German manufacturer Rulmeca.