Our IE4 motors are asynchronous motors that operate according to the induction principle. In this process, the stationary part, called stator, generates a magnetic field and induces a current flow in the moving rotor; the desired rotary motion is generated by interplay between stator and rotor. Energy is lost at various points during transmission and conversion.
overview of optimisation potentials
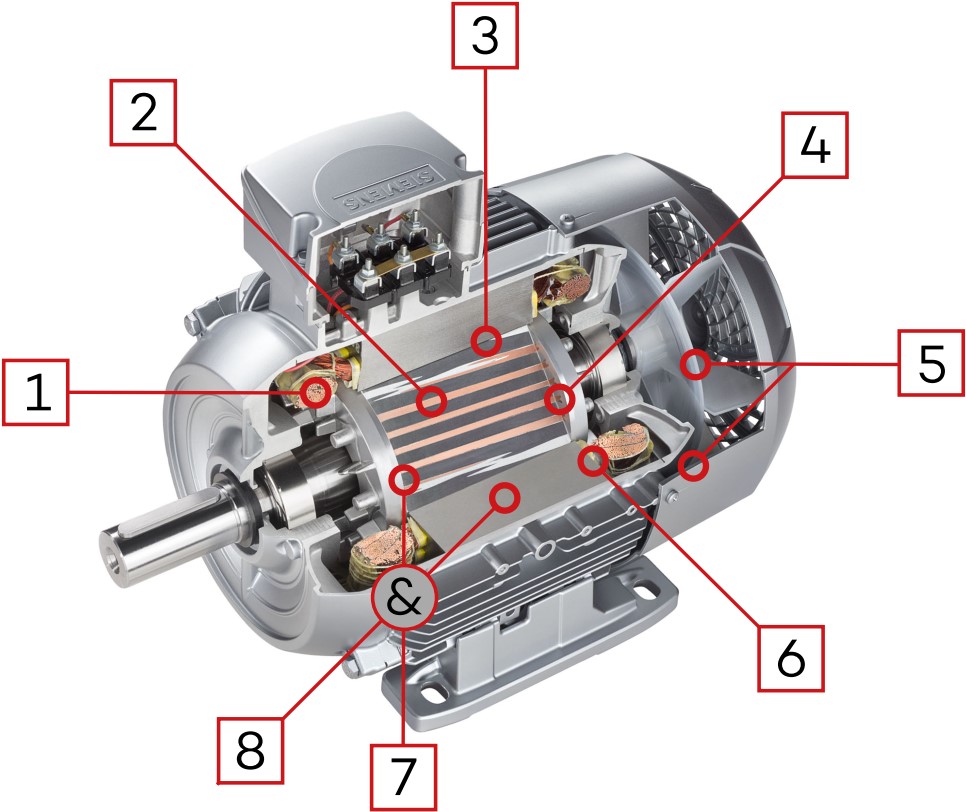
1 | Increased diameter of copper wire reduces ohmic resistance and electricity heat losses in the stator winding. |
2 | Thicker rotor bars and short-circuit rings reduce ohmic resistance and electricity heat losses in the rotor. Effect can be enhanced by using a copper inlay (only visible with rotor bars). |
3 | Reduced air gap between rotor and stator reduces magnetic reluctance. |
4 | Geometrically optimized lamination sheet cutting form in the rotor (visible) and stator (not visible) reduces stray losses. |
5 | Optimized shape of fan wheel and fan cover improves flow of cooling air and reduces aerodynamic drag. |
6 | Longer stator reduces magnetic flux density and heat losses in the iron. Additionally, heat dissipation to the housing improves. |
7 | Thinner electrical laminations in rotor and stator reduce eddy current losses. |
8 | Higher quality electrical steel with improved crystallographic structure in rotor and stator reduces hysteresis losses. |
Current heat losses in the stator
In the stator, many meters of copper wire are wound into coils. Whenever current flows through a wire, it heats up. To save costs, thinner wire is commonly used in mass production of electric motors because it is easier to process. However, thicker wire has lower ohmic resistance. In motors with higher efficiency, the thickness of the copper wires is increased [1] and optimized so that as little energy as possible is lost for heating the winding when the magnetic field is generated.
optimised rotor design
Around the motor shaft is the rotor. The magnetic field generated in the stator induces a current here. This current flows in a circuit, through the rotor bars and short-circuit rings. Optimizing production costs leads to more narrow parts, made only of aluminum. Optimizing for efficiency, thickness and material must be adjusted, e.g. by using copper bars [2], which must be inserted by hand. This reduces resistance in the stator, less waste heat is produced.
A gap between rotor and stator enables rotation, it’s called the “air gap”. Magnetic fields spread poorly in air, so the gap should be as narrow as possible, clearly visible on the picture [3]. Due to less space between the two parts also means that both rotor and stator must be machined more precisely, to avoid rubs during operation. The assembly of the motor must be carried out much more conscientiously as well.
The rotor bars mentioned above are embedded in the rotor’s laminated core, a stack of magnetizable steel sheets. Each of these sheets has holes or slots for the bars. The rotor bars are usually generated from aluminum, which is poured into the holes of the stack of laminations in a liquid state. The shape of the slots thus determines the shape of the rotor bars. As the shape has a great influence on the torque characteristics of the motor, previously common round or rectangular holes have been replaced by sophisticated shapes. In IE4 motors, the shape is optimized for maximum efficiency. The picture unveils an arrow-like shape of the slots [4].
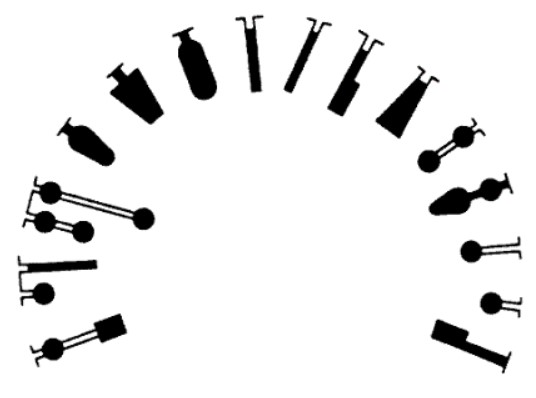
Efficient ventilation
The rotary motion of the motor is transmitted to the application via the motor shaft, shown at the front left of the picture. On the opposite side, the shaft also sticks out from the motor housing and turns a fan, sucking-in air from the rear end and blowing it over the motor surface for cooling purpose. Here, optimization means skillfully balancing. The cooler the motor, the more efficiently it runs. But on the other hand, a larger fan wheel has a higher air resistance and thus consumes more energy. Each manufacturer has its own ideas for adapting the shape of the fan and fan hood [5] to achieve good cooling with as little air resistance as possible.
stator length
Besides optimizations, another way to improve efficiency is to simply increase the size of existing elements. While height of a motor is specified by IEC standard, the length can be chosen by each manufacturer. Many manufacturers therefore increase the stator length for IE4 motors [6]. In this way, the magnetic field can be distributed over a larger area. With the magnetic flux density reduced, the heat losses in the iron are reduced as well. In addition, the contact area to the motor housing also increases, and heat is dissipated more effectively.
Sheet metal quality
A particularly effective method of reducing iron losses is the use of thinner electrical steel sheets with better magnetic properties in stator and rotor. These sheets are so thin in the IE4 motor shown in the picture, so the individual sheets are no longer visible [7]. The crystallographic structure, which determines the magnetizability, is already formed during cooling process in the steel mill. Only a few suppliers are specialized in this steel [8]. Thinner plates require extra work. They need to be rolled-out more often until they are thin, more sheets have to be punched to produce one sheet bundle of the same size, the punching tools have to be renewed more often as thin sheets tend to bend more quickly by blunt tools. If a higher number of sheets is used, the insulating coating on each sheet must also be thinner.
These specific technicalities are a challenge not every manufacturer can meet. You are well-advised to turn to MOLL-MOTOR, as we can supply IE4 motors of our own brand as well as from SIEMENS. A more efficient motor is much more valuable, but the extra cost pays off over the lifetime. The motor will quickly recoup the higher initial cost. Our MOLL-MOTOR sales engineers will be happy to help you calculate the savings.